One of the hardest things I'll ever do is try to explain what Ignition is because it can do so darn many things. This is frustrating for me because I want to tell people all about everything Ignition can do -- and I could overwhelm a person fast. It's sort of like trying to explain what a car is to a pioneer who has never seen one before, and you say, "not only can you drive across the Sierra Nevada mountains in an hour but you have windshield wipers in case it rains, you have this moving map to keep you from getting lost and you can listen to all your favorite music in stereo while you cruise 70mph over the hill." Man, he hasn't even comprehended what a car is yet.
Intro
Rethinking SCADA Software
One of the hardest things I'll ever do is try to explain what Ignition is because it can do so darn many things. This is frustrating for me because I want to tell people all about everything Ignition can do -- and I could overwhelm a person fast. It's sort of like trying to explain what a car is to a pioneer who has never seen one before, and you say, "not only can you drive across the Sierra Nevada mountains in an hour but you have windshield wipers in case it rains, you have this moving map to keep you from getting lost and you can listen to all your favorite music in stereo while you cruise 70mph over the hill." Man, he hasn't even comprehended what a car is yet.
"Softwar" - the future of MES and SCADA

Actually, all these per tag, per client, per designer seat, per database connection licensing models are history. One big SCADA company "graciously" got rid of their per tag licensing model only to replace it with a per screen licensing model. Thanks for the "help" – probably the most liberal licensing model to come along in SCADA in the last ten years (except for Ignition, of course!).
Truth be told, the whole client-server model of MES and SCADA is on an evolutionary dead end. Not my words – those belong to Larry Ellison, except he was referring to IT practices of ten years ago. Softwar is a book about Oracle and Larry Ellison (its CEO and main founder) . It's one of my favorite books because it's a blueprint of things to come in our industry. There's an uncanny parallel between Ellison's predictions of ten years ago for the IT industry (which have come true) and what's happening in our controls industry today. You should read the book.
So what was Ellison saying? He was saying database centricity was the only viable model. He said the client-server model only distributed complexity and was an unsustainable model. He said it was on an evolutionary dead end. As I read those words I was saying "Yea! That's what I've been saying all along!" Only he said it first and history has proven him right.
Ellison was also talking about his rationale for the Oracle eBusiness Suite. He reasoned that all applications at the ERP level should have a common data store, common data schema, common user interface and should deliver common business processes "out-of-the-box." This would prevent data fragmentation, unsustainable support requirements and eliminate the cost prohibitive modifications required to make heterogeneous applications work together (though poorly).
This is exactly what we're doing with the Ignition MES Suite. You haven't seen the whole suite yet – just scheduling, production, downtime and OEE so far. But in the coming year and just beyond, expect to see the most impressive suite of MES functionality available anywhere and completely in alignment with these principles.
We go one step further though with our licensing model because you just pay for the server. Then you can develop with the included web-launched designer, web-launch as many clients as you want, create as many projects as you want, use as many tags as you want and never be constrained again. Everything that applies to our unlimited SCADA suite applies to our MES suite too. Go for it!
What's wrong with MES?

What is MES in the first place? Otherwise known as manufacturing execution system, it's a collection of applications sitting just above PLCs on the plant floor and just below ERP systems like SAP, JD Edwards, or Oracle eBusiness Suite. And therein lies the problem; as a "collection of applications," each one has its own data silo, data format, user interface and support requirements. These are apps like scheduling, production tracking, downtime tracking & OEE, quality assurance, recipe management, genealogy, maintenance maintenance management and a host of others. If you could just get them to play together it would be great.
Most of these applications have been developed by different companies, so getting any sort of consistency and interoperability is nearly impossible. That is especially true of the big "we have it all" vendors because nearly every one of them got their applications by buying smaller companies. So in actuality, each of the parts are incompatible.
Consider for a moment what it would be like if these did play well together. Maintenance management would know what production scheduling was up to and vice versa. If QA was putting product on hold then scheduling would know right away so that they could schedule something else until the problem is fixed. Line operators would know what is planned for the day. There are endless ways to gain efficiencies when every app is seamlessly interconnected by a common data store, common data format, common user interface and uniform support requirements.
A kludge of heterogeneous MES apps is also expensive to install and maintain. Attempting to make apps talk to other apps could cost months of labor for integration, testing and debugging. The IT support required afterward would be beyond burdensome because no app is like any other from a technical standpoint.
When selecting MES software it would be wise then to look at the big picture. First, consider all the apps that your organization could ultimately benefit from and then ensure they form a suite of products designed from the ground up with a common data store, uniform data format, uniform user interface and with uniform support requirements. The payback to your company could be handsome if this simple guideline is followed.
Ignition Mobile - The Backstory

Technology Decisions
Surprised by the Results
Where is the 'c' in MES?

Stuxnet and Common Sense

Today, even a kid could install Ignition

FactorySQL and FactoryPMI were revolutionary products. But they were separate products that had to work with third party products before they could do anything. More than one person got lost in the installation process. But Ignition is another story. The installation process is so simple it's gotten ridiculous.
Outsourcing Development... Not!

Linux SCADA

OPC Xi: Is it Dead Yet?

Whither Silverlight?

Web-based HMI: from 2002 to present day

OPC-UA development from the spec

Building Applications in Earthquake Territory

Hey! Spectrum Controls, Moxa, Online Development, et al

Hey guys, I've got a great idea for you. Why not make an OPC-UA-to-protocolX converter box. Maybe it could be an in-chassis card for PLCs or maybe something like the WebPort 500 (an external DIN rail mount box with serial to various PLCs using various protocols).
I mean, ideally, PLC manufacturers would build OPC-UA right into their PLCs. I say this because it's extremely secure, platform neutral and it accommodates any shape data structure. But you and I both know why that might take a very long time. So that presents quite an opportunity for you.
Right now, Modbus TCP is the lingua franca (universally spoken language) and most PLC manufacturers build it right into their PLCs in addition to their own primary protocols. I love Modbus TCP because it's open, fast, simple and ubiquitous. But it's not so secure and as far as I know it only supports elementary data types. OPC-UA is destined to be its successor since it answers these and a host of other problems.
The recent OPC interop conference in Germany (which we recently sent a couple of developers to) was a good indication of what to expect of OPC-UA. The number of OPC-UA servers and clients tested at the conference nearly tripled from just a year before – showing that the use of OPC-UA in the industry is growing fast.
So I bring it up now. I think the OPC-UA converter box (or in-rack card) is a great idea. If I was in the hardware business I wouldn't be telling you this – I'd be doing it myself.
Python - The Cartoon
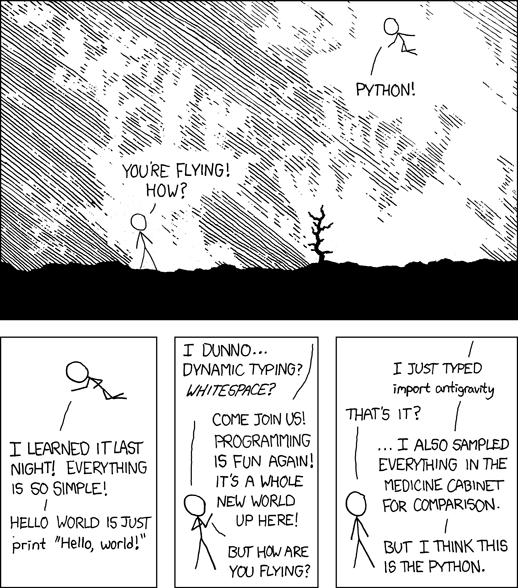
For those of you who missed Carl's comment of October 13th here is a comic strip that he referred to. Apparently, my reaction to Python is pretty universal (you can read about my reaction in my post of October 13th).
Here's the thing, in any language the most tedious part is likely to be the GUI programming. But when you program Python in Ignition all the heavy lifting is done for you because Ignition makes GUI development a snap. It also handles deployment, security, authentication, database connections and data caching, single file backup, PLC connectivity and I could go on for paragraphs. So with your scripts all you have to concentrate on is the immediate specialized task at hand. That makes development fast. Really fast.
But more than that, it makes development fun. Nothing like the grueling days of VBA (which by the way is obsolete, is filled with security holes, and is an ugly language).
Ignition - What's the Catch?

This happens so often that I thought I better comment on it. Yesterday I was talking with one of our users who happens to be so jazzed on Ignition that he shows his plant, which uses it, to other people all the time. At the end of a recent showing he told me "they were just standing there drop-jawed but kept asking 'what's the catch?'"
The Sheer Joy of Python

I decided to take on a little project just for fun and used Python (naturally since that is Ignition's embedded "scripting" language) to do it. I decided to download the Python IDLE IDE (Integrated Development Environment) to see if I could speed development a bit. The whole download from the www.python.org website and its subsequent installation only took maybe three minutes (it's free too). It took me a minute or two to figure out how to make it come up in the editor mode rather than the console mode but once I got beyond that I was amazed at how fast I could write a lot of functionality.
I'll tell you a little secret, I googled things I wanted to do and then cut and paste example code into the editor. Then I made a few obvious changes and bingo, it just worked! Then I cut and paste that code into Ignition and it worked.
It became immediately obvious to me that I could even write drivers this way in a pinch. This wouldn't be the recommended way because we have a Java API for third-party developers that would be better integrated. But in a pinch where you need something quick and particularly for simple one-off protocols this would be a good (and fun) choice.
Python is forgiving and intuitive. It has dynamic type casting so you just code away and don't worry about that. The language is easy to read so when you look at another person's code you usually can tell exactly what's being done. But don't be fooled by this ease of use because Python is fully object oriented and in the case of the flavor we use in Ignition (Jython), can drill right down into the Java code. There is no compiling either, just run the code.
I mentioned all this to some of our developers yesterday and they lit up. They reminisced at programming when they were just kids and the sheer joy it brought to them. They said that is what Python does for them now. You can do so much, so fast, totally hassle free. In fact, one of them uses Python for all types of quick tasks that would otherwise be tedious.
I realized that this is what I experienced as well, the sheer joy of programming in Python.
Running Ignition on HP-Unix???

Then there is the case of one customer who knew us from the days of FactoryPMI and FactorySQL who waited until Ignition was ready because they insisted on running on Macs.
The Linux crowd is really starting to grow and I expect it to dominate on the plant floor eventually. In fact, I have this little blue box from Eurotech on my desk running Ignition on Linux. That little box is good for -40 to +85 degC so you can put it on the plant floor or in the field without any air conditioning whatsoever. And it only consumes 3 watts of power so it's perfect for solar applications. Pretty cool!
As I've mentioned before, I consider each and every Windows version (or even different service packs) a different platform as well, despite apparent similarities. I see a lot of industrial software that isn't supported on Vista or Windows 7 or even XP SP3. But by using Java, we don't care what the platform is being used, for the server or for the clients, and that removes one huge headache for most people.
Where's the price?

How many patches did that take???

Why Java?

Few people know that Java is the most popular programming language in the world (See the TIOBE Programming Community Index for September 2010). Java runs on more types of consumer and embedded devices, smart cards, ATMs, thin clients, PCs, servers, and mainframes than any other language.
Additionally, Java is the "write once, run anywhere" language. This is a major reason we selected Java. By writing Ignition in Java it runs equally well on Linux as it does on OSX, Windows or Solaris. Come to think of it, isn't every version of Windows a different platform? Well, Java spans them all. We don't care who wins the operating system wars or even if no one does.
Java is also highly resistant to viruses. Java appears to have been developed with security as a first concern rather than as an afterthought patch-up. That makes it ideally suited to the industrial environment.
With over five million Java programmers (which makes Java the largest developer community) it is far easier to hire software developers than for other languages, especially right out of school.
Rather than following the flock (look at it, every other major HMI company requires Windows) we took a step back and evaluated what language provided the most portability, security, stability and support—and Java was the clear winner.
OPC-UA - Why change now?

Legacy OPC is based on Microsoft's COM technology which has been deprecated for years now (The software definition of deprecation is "software features that are superseded and should be avoided") . Due to the large install base of programs that use the technology Microsoft still supports it. But moving forward Microsoft has signaled neither continued support nor intention not to do so.
The COM technology that legacy OPC depends on has also proven to be a huge security issue. This is so much the case that it has undergone a massive evolution to try to mitigate the factor and in doing so programs that once worked sometimes cease to work after an OS upgrade or patch. This is such a headache that one company delivered seminars around the country teaching people how to deal with COM/DCOM. In fact, the OPC tunnelers offered by a number of companies are a solution to this COM quagmire.
OPC-UA was designed to address these issues and a number of others. It leverages modern security and performance techniques. It can be scaled down to embedded devices or up to the enterprise level. Soon you could expect to connect to PLCs, barcode scanners, flowmeters and practically any other plant floor device directly using native OPC-UA protocol. That would get rid of the headache of a gazillion device drivers. Embedded device manufactures can buy the OPC-UA stack for embedded devices if writing their own stack seems formidable. I believe it's only a matter of time before we see this happen. That's how legacy OPC came to be.
OPC-UA offers IT industry standard authentication and encryption. This is a particularly important consideration when you consider the fact that plant floors increasingly are no longer islands. Consider the recent Stuxnet virus that specifically targets Siemens HMIs.
Unlike legacy OPC, OPC-UA can run on any OS, which might not seem important now, but in the future could be an important factor. We've run into an increasing number of US companies that refuse to run industrial applications on Windows and some of these are large companies. I'm not advocating one way or the other - I'm just commenting on what I see.
COM and DCOM go back to 1994 and there are roots even earlier. OPC-UA is a "now" technology which will probably have longevity since it is based on proven IT standards.
So what should you do moving forward? Clearly, new installations should be OPC-UA or you risk doing it twice. But what about those legacy installations? Sure, if it's working then leave it alone. But be very cautious of any OS upgrades or patches. One customer had automatic updates turned on and in the morning not one single HMI terminal worked, effectively shutting down a large company for the better part of a day.
That next project probably presents the most opportune time to made the move to OPC-UA.
Get IT On Your Side and They'll Seal the Deal For You

As you expand past plant floor controls you begin to enter into the domain of IT. But when you do so you will begin to work with IT folks. Believe me, you want IT on your side or your project will end up on a data island which is useless in an enterprise system.
So how do you do that? Well, first of all you better find out what hardware and software the IT department is willing to support. When I make initial contact with IT folks, I always ask what technology they use. Then I assure them we’ll work with that. This generally makes them very happy. You have to learn to work with them within their envelope. You're not in a position to try and cram something else down their throat. It is only by standardization that they can support huge corporate networks without the job becoming onerous.
The next thing I do is use their terms and refer to the technology they are currently using. If the system you are proposing isn't something they are familiar with or if it uses 1990's technology like DCOM, then you better ditch it and find something else. In short, if they can't relate to it without a bunch of specialized training (which isn't likely to happen) then your project is probably going to die.
But the reverse is true if you can talk their terms and they can wrap their arms around the technology.
IT Could Be Your Best Friend For Sales
In this case, IT is likely to be your biggest proponent and can help you get your project pushed through. I've personally been involved in these situations many times. In one case I had the buy-in of the plant manager, maintenance manager and production manager but I said "now let's get together with you IT department."
The plant manager said "are you SURE you want to do that?" and I said "Yes."
At the start of the meeting the two IT guys had their arms crossed and looked resentful. First I asked them what relational database they used and they said MSSQL Server indignantly. I said great, that's what we use and they perked up a bit.
Then I went to the white board and laid out the system in terms I knew would be acceptable to them. They asked a lot of questions but I answered each in alignment with technology I knew they already were using. Somewhere in the middle of this I saw them flip from being adversarial to helpful. They started asking things like "When do you need this by?", "How much memory do you need?", "Can we run it on a virtual machine?" and in fact they became allies which sealed the deal.
It is an amazing thing to watch how fast EVERYONE else buys-in when IT does. Like I say. You better have them on your side.
Modbus TCP - Lingua Franca

Lingua franca = a common language used by speakers of different languages.
The perfect complement to PLCs

You might ask how it is they’re even related. For one thing, relational databases can sort of be an extension of PLC memory. Live values can be mirrored there bi-directionally. Historical values and events can be recorded there as well. But operators and managers can interact with them too. It’s been over 20 years of working, living, breathing and thinking PLCs, but over the last six years I’ve delved heavily into SQL and learned a lot about relational databases. I’ve discovered that working with SQL is remarkably similar to working with PLCs and ladder logic.
SQL has four basic commands and about a hundred different modifiers that can be applied to each. These can be applied in various ways to achieve all types of results. Here’s an example. Imagine effluent from a wastewater plant with its flow, PH and other things being monitored and logged. That’s what you typically see. But now let’s associate other things with these, such as, discrete lab results, the name of the persons who did the lab work, the lab equipment IDs and calibration expiration dates, who was on shift at the time and the shift just prior, what their certification levels were, what chemicals where added and when, who the chemical suppliers were, how long the chemicals sat before use, and so forth ad infinitum. All of this becomes relational data, meaning that if it’s arranged properly in tables you can run SQL queries to obtain all types of interesting results. You might get insight into the most likely conditions which could result in an improper discharge so it can be prevented in the future.
In my explorations of SQL, I found myself looking at the layout of my tables and evaluating the pros and cons of each layout. I massaged them, turned them on their side, upside-down, and finally ended up with the most appropriate arrangement for my application. And similar to PLC programming, I explored innumerable what-if scenarios. I was struck by the amazing similarity in my approach to developing solutions for PLCs. This has been a lot of fun — in fact exhilarating — just like PLCs used to be. It’s the next logical progression you know.
SQL is a high level language that isn’t very hard to learn and you can be very clever with it. I prefer to think of it as a natural extension to my PLC programming skills. Now that you have the machinery running, what did it do? Furthermore, relational databases and SQL pull people and processes together. Machines don’t run alone. They’re merely part of a containing process and that process was devised by people. SQL and relational databases form the bridge to integrate processes, machinery and people together. I don’t believe a COTS (commercial-off-the-shelf) package can do it any more than you could offer a COTS palletizer program and have it be of any use. It just doesn’t work that way. Every machine is different. And every business process is different. That’s where the SQL comes in. It has to duplicate or augment existing process flows and these are intimately connected to the machinery. And that’s why the PLC programmer is best suited to implement solutions involving PLCs and relational databases.
So where do you start? I would suggest picking up a book at the bookstore like one of those dummies books. Then download and install the open-source MySQL database server along with the MySQL Administrator and Query Browser. It only takes a few minutes to install and then start playing. You can read about a LEFT JOIN or INNER JOIN but typing one in and observing the results is worth about 1,000 words. At the end of an evening you’ll probably be very excited with all of your new found knowledge and be thinking of endless ways to employ it in your own field of practice. Happy SQLing!
Process Historians vs. SQL Databases

While there may be some specialized domains where process historians have a niche, they are not a practical choice for most industrial applications. In effect, historian vendors are saying your Toyota Camry is inappropriate transportation because it is incapable of going 180 mph or finishing the quarter mile in under 10 seconds.
An Ill-Founded Rumor
The rumor denigrating relational databases for poor throughput is baseless. A standard, off-the-shelf Microsoft SQL Server coupled with Ignition's SQL Bridge Module can log in excess of 100,000 tags per second using a desktop machine. In all likelihood, other factors such as the industrial network would become bottlenecks before the database does. Furthermore, today’s generation of SQL relational databases are designed to scale gracefully to power high-volume website traffic, whose load peaks dwarf those of industrial controls applications.
Data compression is an area where process historians do score a point. However, even this consideration can be handled with standard off-the-shelf SQL relational databases. Take a look at the MySQL 5.0 Archive Storage Engine which achieves on average a four to one compression ratio. Proprietary process historians may beat that, but let’s get back to the point of practicality. Hard disk space is so cheap these days that even considering this point is becoming an anachronism. For the rare application that demands it, table compression coupled with intelligent data logging allow databases to compete even in this regard.
One crucial question that process historian vendors omit is: what are IT departments willing to support? When I make initial contact with IT folks, I always ask which relational database they use. Then I assure them we’ll work with that. This generally makes them very happy. Believe me, you want IT on your side or your project will end up on a data island which is useless in an enterprise system. Think of it from their point view; they have the training and tools, generally, to support just one type of database. With these tools and training they can support the database with scheduled backups, tuning and other maintenance.
Support, Relational Data, and Cost Factors
Okay, we’ve heard process historian rants about relational databases; let’s talk about the downside of process historians. Let’s start with support. Just check the Amazon bookstore for any one of the proprietary process historians and you’re likely to come up empty handed. On the other hand, check for “SQL configuration” and you’ll come up with hundreds of books. How about finding people to support these proprietary systems? Good luck.
Then there is the concern about supporting relational data with a process historian. Frankly, the middleware layer is all about relational data. Time-series data, which is what process historians deal with, is just a fraction of what is needed in the middleware layer. Correlating batches, shifts, inventory, orders, downtime, quality, etc., is purely relational in nature, and these are the features that today’s enterprise integration projects demand.
What about a cost comparison? The process historian is going to be 10 to 30 times the cost of a relational database using a driver like the Ignition SQL Bridge Module depending on the number of tags required. The controls industry is still backwards on this point and prefers to price its software per tag as though the extra tags cost money to manufacture.
In summary, we’re talking about practical choices. The Ferrari may be great fun, but do you need a $500,000 vehicle to drive the kids to school or would the Camry suffice? Likewise, do you need a $60,000 process historian to log data? A relational database makes a great historian, but the reverse isn’t true. A process historian cannot process relational data. For the vast majority of systems, a relational database has more than enough power to service the historical and relational data requirements, making it not just the practical, but the wise choice.
"Sounds too good to be true."
The Three-Minute Misconception

I almost bust a gut the other day. I was talking with an industry analyst and asked him if he'd seen our website. He said “yes” so I asked him what he took away from it. He said it looked like a great solution for lightweight applications. Incredulously, I asked him what on our site led him to the belief the software was best suited for “lightweight” applications. His response? “It only takes three minutes to install!”
Wow! If I knew that our three-minute install would be interpreted that way, I would have directed our developers install delay loops into our installation process so that it would take four hours or four days like everyone else's does!
All joking aside, I set the record straight by citing some of the massive deployments people are doing with Ignition. He soon saw, that in fact, a single Ignition server can deploy hundreds of clients, connect to dozens of SQL databases of practically any flavor, can launch one (or a dozen) concurrent developer stations, perform as a full historian and reporting engine, run on any OS platform – and a whole lot more for a single, affordable price. But he also saw it could perform as a lightweight system too.
The truth is, when you are used to dealing with 1990’s technology, DLL hell, and systems that have been over-patched by an endless string of programmers who have come and gone, you are bound to be shocked when you see what modern technology can do.